Heat Treatment and Press Forming Production Operations
Heat treatment operations of Atommash are used for heat treatment of products in various sizes: from fasteners blanks, base metal samples and test welded joints to assembled steam generators and reactor vessels. The production site is equipped with plate-levelling and plate-bending machines. The three-roll plate bending machine with a top roll diameter of 1,800 mm makes it possible to bend plates up to 4,500 mm wide and up to 350 mm thick.
Russia’s only 15,120 ton-force capacity hydraulic forming machine allows to stamp heads with a diameter of up to 5,000 mm and a plate thickness of up to 400 mm.
Equipment
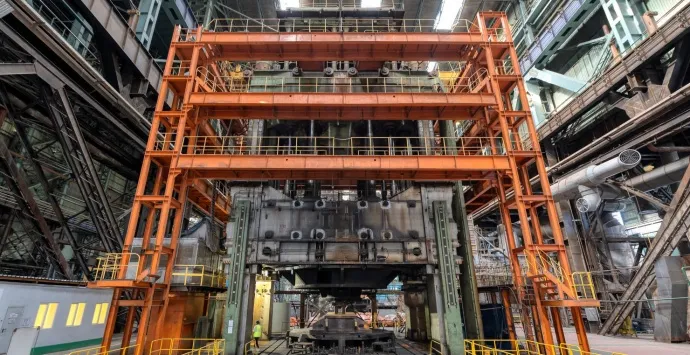
Hydraulic forming machine
Description | Double-acting hydraulic forming machine has no analogues in Russia. Equipment with a maximum capacity of 15,000 ton-force is used for forming heads with a plate thickness of up to 380 mm and a diameter of up to 5,000 mm.
|
Main characteristics |
Maximum forming force: 15,000 tf
Drawing slide force: up to 10,080 tf Blankholder slide force: up to 5,000 tf Slider stroke: 5,200 mm Distance between columns along the front of the press: 10,500 mm Plan dimensions: moving table - 9,000 mm × 9,000 mm blankholder slide - 9,000 mm × 9,000 mm drawing slide - 6,500 × 6,500 mm |
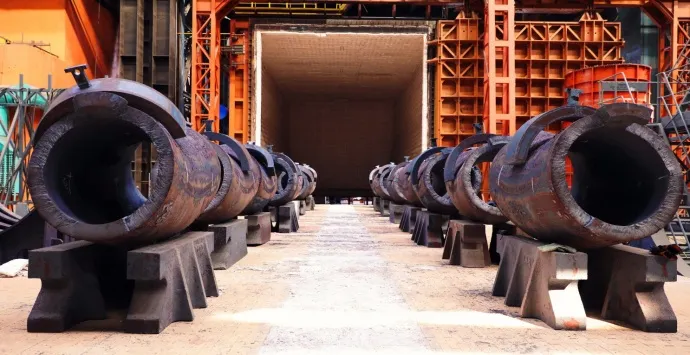
Chamber gas furnace with bogie hearth
Description | The furnace is used for heat treatment of equipment for nuclear power plants. It allows to carry out quenching and tempering of large-sized items, including reactor and PGV steam generator vessels as an assembly. |
Main characteristics |
Overall dimensions: 9,000 × 10,000 × 25,000 mm
Maximum operating temperature: 9,200 °С Maximum charge weight: 600 t
|
Production Capabilities
01
Possibility of heat treatment of large-sized products
02
Development and implementation of new stamping technologies
The press forming section allows you to stamp various types of products for the nuclear industry, thermal power engineering and the oil and gas industry.
Production meets modern standards. Finished equipment is delivered to different parts of the world.
Production meets modern standards. Finished equipment is delivered to different parts of the world.